再生材対応で短納期・高精度を実現した成形ライン構築事例STORY02
環境対応が求められる製品開発の現場では、再生材の活用と短納期・高精度の両立が大きな課題となります。 本事例では、埼玉県の電機部品メーカーY社様のご要望に対し、当社がどのように現場と連携しながら対応させて頂いたのかをご紹介いたします。
お客様の課題と背景BEFORE
「対応可能な成形メーカーが見つからない」
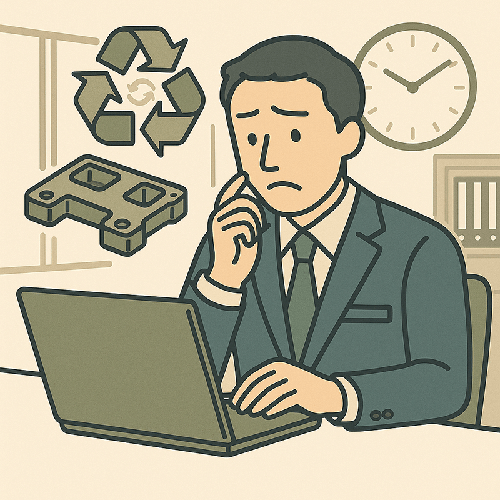
埼玉県の電機部品メーカーY社では、次世代住宅設備に使用する再生プラスチック部品の試作が急務となっていました。 要件は「外観のヒケや変形なし」「±0.1mmの寸法公差」「試作納期2週間以内」。精密さとスピードを両立する、極めて難易度の高い依頼です。
成形メーカー5社に相談を持ちかけたものの、いずれも「再生材では精度が出せない」「納期的に対応不可」と断られ、プロジェクトは暗礁に。 社内では製品リリースの遅延が現実味を帯びはじめ、開発リーダーの佐藤様(仮名)は打つ手を失いかけていました。
そんな中、「再生材の精密成形に対応できる」と紹介されたのが、当社アルファでした。
ご相談ときっかけDISCOVERY
「再生材でも精度が出る金型を作れますか?」
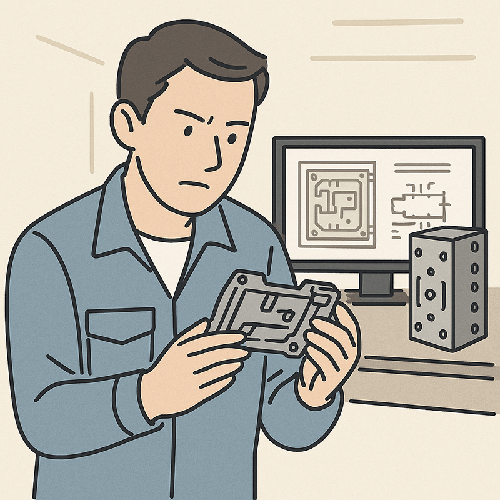
ご連絡をいただいたのは、佐藤様ご本人。ご事情を伺い、その日のうちに再生材の仕様と図面の確認、成形条件のリスク評価を実施しました。
私たちアルファでは、「再生材だから難しい」とは考えません。 環境対応と短納期を“両立できないもの”とせず、日常的に両立する体制と技術を標準装備しています。
過去の実績から短納期での対応が可能であることをお伝えしたところ、「他社が断る中で即日判断してくれるのは御社だけ」と高く評価され、 正式にご依頼いただく運びとなりました。
現場密着のカスタム対応ACTION
“再生材のクセ”に即応するチーム力
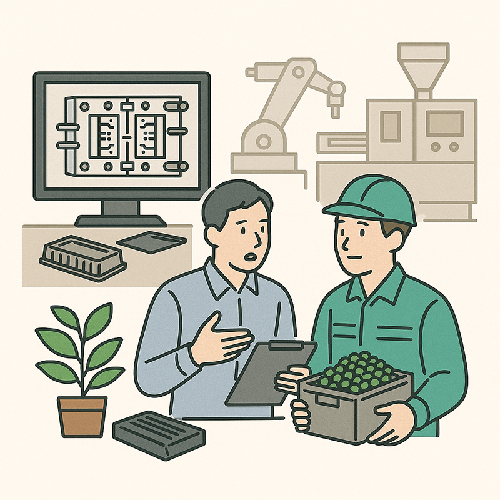
提供された再生材を当社で物性評価した結果、微細な添加物の影響による反りや収縮のリスクが明らかになりました。 設計・製造・品質それぞれの部門が即時に連携し、解決策を協議。
設計担当・中村(仮名)とCAM担当・田辺(仮名)が逃げ構造を加えた金型設計をその日のうちに完了し、 外注金型メーカーへ即時データ送信。翌日には金型改修を完了。 成形オペレーター・山本誠(仮名)の緻密な調整により、±0.1mm以内の寸法精度を達成しました。
通常は1週間以上かかる工程を、わずか48時間でクリア。 これを可能にしているのが、“素材特性に応じて即対応できる体制と判断力”です。
成果と変化AFTER
「この納期、この精度…正直驚きました」
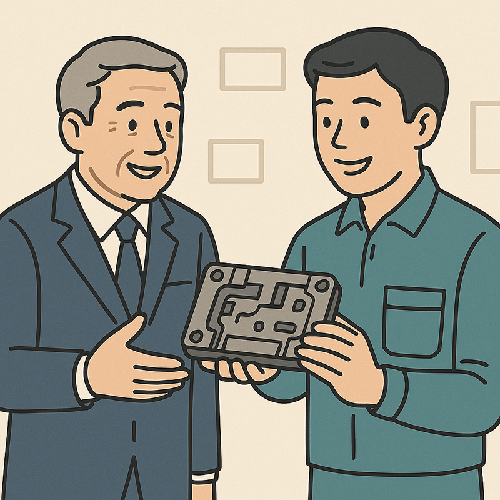
試作完成品をご覧になった佐藤様は、「精度・外観・材料安定性、すべてにおいて想定以上」とコメント。 社内の品質部門による承認も無事通過し、同シリーズ8型番すべての正式量産を当社へご発注いただきました。
短納期・高精度・再生材対応という“三重難題”に対して、社内外から高評価を得る成果となりました。
今後の展開と提言FUTURE
“できない”を“できる”に変える、当社の標準対応力
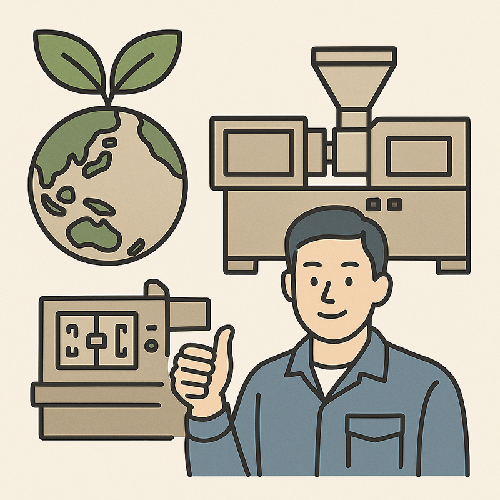
再生材やバイオプラスチックなど、成形が難しいと言われる環境対応材料に対しても、当社では「設計」「成形」「品質」が一体で動く仕組みを構築しています。 難易度の高い依頼こそ、当社の“つくる力”が発揮される領域です。
「図面がない段階でも相談できますか?」——もちろんです。 設計段階からの技術的可否判断、成形条件の最適化、量産見据えた試作まで、すべてにおいて伴走します。
再生材対応に悩む方こそ、ぜひ一度、当社にご相談ください。